![]() |
磁翻板液位计 | ||
![]() |
磁浮球液位计 | ||
![]() |
浮球液位开关、控制器 | ||
![]() |
法兰式液位变送器 | ||
![]() |
智能电容式液位计 | ||
![]() |
投入式液位计、变送器 | ||
![]() |
雷达液位计 | ||
![]() |
玻璃管液位计 | ||
![]() |
锅炉双色水位计 | ||
![]() |
电磁流量计 | ||
![]() |
涡街流量计 | ||
![]() |
液体涡轮流量计 | ||
![]() |
超声波流量计 | ||
![]() |
孔板流量计 | ||
![]() |
金属管浮子流量计 |
全国销售热线:400-9280-163
电话:86 0517-86917118
传真:86 0517-86899586
销售经理:1560-1403-222 (丁经理)
139-1518-1149 (袁经理)
业务qq:2942808253 / 762657048
网址:https://www.harzkj.com
电话:86 0517-86917118
传真:86 0517-86899586
销售经理:1560-1403-222 (丁经理)
139-1518-1149 (袁经理)
业务qq:2942808253 / 762657048
网址:https://www.harzkj.com
液位仪表、流量仪表等自动化仪表故障时标准处理流程(附图)-九游会ag登录
发表时间:2016-09-13 点击次数: ag九游会官方网站的技术支持:15601403222
尤其是现代化的化工企业自动化水平越来越高 ,由于石油化工生产操作管道化、流程化、全封闭等特点,生产中的工艺操作与检测仪表密切相关,自动化仪表的稳定性与可靠的质量在其中非常重要,工艺人员通过检测仪表显示的各类工艺参数,诸如反映温度、物料流量、容器的压力和液位、原料的成分等来判断工艺的生产是否正常,产品的质量是否合格,根据仪表的指示加量或减产,甚至停车。
一般情况下仪表指示出现异常情况(指示偏高、偏低,不变化,不稳定等),本身包含两种因素:
*先是工艺因素,仪表正确的反映出工艺的异常情况;
其二是仪表因素,由于仪表(检测环境)某一环节出现故障导致工艺参数指示与实际不符。
这两种因素总是混淆在一起,很难马上判断出故障到底出现在哪里。仪表维护人员要提高仪表故障判断能力,除了对仪表原理、结构、性能特点熟悉外,还需熟悉测量系统中的每一个环节。
同时,对工艺流程及工艺介质的特性、化工设备的特性应有所了解,这能帮助仪表维护人员拓展思路,由助于分析和判断故障现象。
仪表故障判定思路
◆ ◆ ◆
温度检测故障判断
故障现象:温度指示不正常,偏高或偏低,或变化缓慢甚至不变化等。
以热电阻作为测量原件进行说明。
*先是应了解工艺状况,应询问工艺人员被测介质的情况及仪表安装位置,是在气相还是液相或其他的工艺状况。
因为是正常生产中的故障,不是新安装的热电阻,是用可以排除热阻线极性接反。排除上述因素后可以按下图的思路进行判断和检查。
y表示是 n表示否
温度仪表系统常见故障处理:
(1)温度突然增大:此故障多为热电阻(热电偶)断路、接线端子松动、(补偿)导线断、温度失灵等原因引起,这时需要了解该温度所处的位置及接线布局,用万用表的电阻(毫伏)档在不同的位置分别测量几组数据就能很快找出原因。
(2)温度突然减小:此故障多为热电偶或热电阻短路、导线短路及温度失灵引起。要从接线口、导线拐弯处等容易出故障的薄弱点入手,一一排查。现场温度升高,而总控指示不变,多为测量元件处有沸点较低的液体(水)所致。
(3)温度出现大幅度波动或快速震荡:此时应主要检查工艺操作情况(参与调节的检查调节系统)。
◆ ◆ ◆
流量检测故障判断
故障现象:流量计指示不正常,偏高或偏低,或指示为零、指示波动。
以差压流量变送器为例(孔板流量计)仪表维护人员在处理故障时,应向工艺操作人员了解情况,了解工艺情况,如被测介质的情况,机泵情况以及工艺流程等。通过对工艺开车情况的详细了解,故障处理可以按下图所示思路进行判断和检查。
流量仪表系统常见故障处理:
(1)流量指示值小:一般由以下原因造成:检测元件损坏(零点太低。;显示有问题;线路短路或断路;正压室堵或漏;系统压力低;参与调节的参数还要检查调节器、调节阀及电磁阀。
(2)流量指示大:主要原因是负压室引压系统堵或漏。变送器需要调校的可能不大。
(3)流量波动大:流量参数不参与调节的,一般为工艺原因;参与调节的,可检查调节器的pid参数;带隔离罐的参数,检查引压管内是否有气泡,正负压引压管内液体是否一样高。
◆ ◆ ◆
压力检测故障判断
故障现象:某泵出口指示不正常,偏高或偏低,或指示为零或不变化。
以电动压力变送器为例。
*先应了解被测介质是气体还是液体,了解工艺开车情况和简单工艺流程,根据对工艺情况的了解和仪表故障现象来进行仪表故障判断和处理。有关故障判断及处理可按下图的思路来进行检查。
压力仪表系统常见故障处理:
(1)压力突然变小、变大或指示曲线无变化:此时应检查变送器引压系统,检查根部阀是否堵塞、引压管是否畅通、引压管内部是否有异常介质、排污丝堵及排污阀是否泄漏等。冬季介质冻也是常见现象。变送器本身故障可能性很小。
(2)压力波动大:这种情况*先要与工艺人员结合,一般是由操作不当造成的。参与调节的参数要主要检查调节系统。
◆ ◆ ◆
液位检测故障判断
故障现象:液位指示不会变化,偏高或偏低,或无指示。
以双法兰液位变送器为检测仪表。
*先要了解工艺状况、工艺介质,被测对象是原稳塔、还是储罐(槽)、反应器。用双法兰液位变送器测量液位,往往同时配置就地显示液位计,工艺操作人员以就地显示液位计为参照判断差压式液位变送器所测量值指示偏高或偏低,因为就地显示液位计比较直观。
而仪表维护人员应根据工艺状况和仪表故障现象进行判断和检查。有关液位(物位)检测故障判断思路可以参照下图进行。
液位仪表系统常见故障处理:
(1)液位突然变大:主要检查变送器负压室引压系统是否堵、泄漏、集气、缺液等。
灌液的具体方法是:
按照停表顺序先停表;
关闭正负压根部阀;
打开正负压排污阀泄压;
打开双室平衡容器灌液丝堵;
打开正负压室排污丝堵;此时液位指示大。
关闭排污阀;
关闭正负压室排污丝堵;
用相同介质缓慢灌入双室平衡容器中,此时微开排污丝堵排气;
直至灌满为止,此时打开正压室丝堵,变送器指示应回零位。
然后按照投表顺序投用变送器。
(2)液位突然变小:主要检查正压室引压系统是否堵、漏、集气、缺液、平衡阀是否关死等。
检查引压系统是否畅通的具体方法是停变送器,开排污阀,检查排污情况(不能外泄的介质除外)。
(3)总控室指示与现场液位不相符:*先判断是不是现场液位计故障,此时可以人为增大或降低液位,根据现场和总控指示情况具体分析问题原因(现场液位计根部阀关闭、堵塞、外漏易引起现场指示不准)。
可以通过检查零点、量程、灌液来恢复液位正常。
如果仍不正常,可通知工艺人员现场监护拆回变送器打压调校。
(4)液位波动频繁:*先和工艺人员结合检查进料、出料情况,确定工艺状况正常后,可通过调整pid参数来稳定。
具体方法是:调节阀投手动状态,先调整设定值与测量值一致,使液位波动平稳下来,再慢慢调整调节阀开度,使液位缓慢上升或下降,达到工艺要求,再调整设定值与测量值一致,待参数稳定后调节阀投自动。
◆ ◆ ◆
简单控制系统故障判断
故障现象:控制系统不稳定,输入信号波动大。
以流量简单控制系统为例,控制系统由双法兰液位变送器、单回路调节器和带电气阀门定位器的气动薄膜调节阀组成。
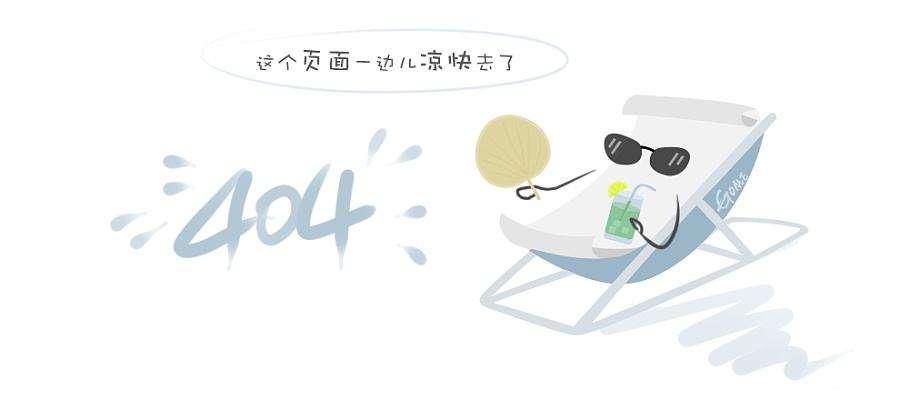
在处理这类故障时,仪表维护人员应很清楚该流量控制系统的组成情况,要了解工艺情况,如工艺介质,简单工艺流程,是加料流量还是出料流量或是塔的回流量。处理故障步骤详见下图。
总之,一旦发现仪表参数有些异常,*先与工艺人员结合,从工艺操作系统和现场仪表系统两方面入手,综合考虑,认真分析,特别要考虑被测参数和控制阀之间的关联,将故障分步分段判定,也就很容易找出问题所在,对症下药解决问题。(本文由九游会ag登录-ag九游会官方网站整理发布,如您在使用仪表的过程中遇到任何问题,都可以致电我司的国内销售服务热线:0517-86917118,我们会有**人员为您答疑解惑)
一般情况下仪表指示出现异常情况(指示偏高、偏低,不变化,不稳定等),本身包含两种因素:
*先是工艺因素,仪表正确的反映出工艺的异常情况;
其二是仪表因素,由于仪表(检测环境)某一环节出现故障导致工艺参数指示与实际不符。
这两种因素总是混淆在一起,很难马上判断出故障到底出现在哪里。仪表维护人员要提高仪表故障判断能力,除了对仪表原理、结构、性能特点熟悉外,还需熟悉测量系统中的每一个环节。
同时,对工艺流程及工艺介质的特性、化工设备的特性应有所了解,这能帮助仪表维护人员拓展思路,由助于分析和判断故障现象。
仪表故障判定思路
◆ ◆ ◆
温度检测故障判断
故障现象:温度指示不正常,偏高或偏低,或变化缓慢甚至不变化等。
以热电阻作为测量原件进行说明。
*先是应了解工艺状况,应询问工艺人员被测介质的情况及仪表安装位置,是在气相还是液相或其他的工艺状况。
因为是正常生产中的故障,不是新安装的热电阻,是用可以排除热阻线极性接反。排除上述因素后可以按下图的思路进行判断和检查。
y表示是 n表示否
温度仪表系统常见故障处理:
(1)温度突然增大:此故障多为热电阻(热电偶)断路、接线端子松动、(补偿)导线断、温度失灵等原因引起,这时需要了解该温度所处的位置及接线布局,用万用表的电阻(毫伏)档在不同的位置分别测量几组数据就能很快找出原因。
(2)温度突然减小:此故障多为热电偶或热电阻短路、导线短路及温度失灵引起。要从接线口、导线拐弯处等容易出故障的薄弱点入手,一一排查。现场温度升高,而总控指示不变,多为测量元件处有沸点较低的液体(水)所致。
(3)温度出现大幅度波动或快速震荡:此时应主要检查工艺操作情况(参与调节的检查调节系统)。
◆ ◆ ◆
流量检测故障判断
故障现象:流量计指示不正常,偏高或偏低,或指示为零、指示波动。
以差压流量变送器为例(孔板流量计)仪表维护人员在处理故障时,应向工艺操作人员了解情况,了解工艺情况,如被测介质的情况,机泵情况以及工艺流程等。通过对工艺开车情况的详细了解,故障处理可以按下图所示思路进行判断和检查。
流量仪表系统常见故障处理:
(1)流量指示值小:一般由以下原因造成:检测元件损坏(零点太低。;显示有问题;线路短路或断路;正压室堵或漏;系统压力低;参与调节的参数还要检查调节器、调节阀及电磁阀。
(2)流量指示大:主要原因是负压室引压系统堵或漏。变送器需要调校的可能不大。
(3)流量波动大:流量参数不参与调节的,一般为工艺原因;参与调节的,可检查调节器的pid参数;带隔离罐的参数,检查引压管内是否有气泡,正负压引压管内液体是否一样高。
◆ ◆ ◆
压力检测故障判断
故障现象:某泵出口指示不正常,偏高或偏低,或指示为零或不变化。
以电动压力变送器为例。
*先应了解被测介质是气体还是液体,了解工艺开车情况和简单工艺流程,根据对工艺情况的了解和仪表故障现象来进行仪表故障判断和处理。有关故障判断及处理可按下图的思路来进行检查。
压力仪表系统常见故障处理:
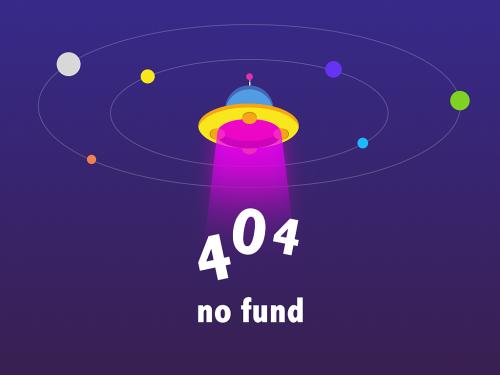
(1)压力突然变小、变大或指示曲线无变化:此时应检查变送器引压系统,检查根部阀是否堵塞、引压管是否畅通、引压管内部是否有异常介质、排污丝堵及排污阀是否泄漏等。冬季介质冻也是常见现象。变送器本身故障可能性很小。
(2)压力波动大:这种情况*先要与工艺人员结合,一般是由操作不当造成的。参与调节的参数要主要检查调节系统。
◆ ◆ ◆
液位检测故障判断
故障现象:液位指示不会变化,偏高或偏低,或无指示。
以双法兰液位变送器为检测仪表。
*先要了解工艺状况、工艺介质,被测对象是原稳塔、还是储罐(槽)、反应器。用双法兰液位变送器测量液位,往往同时配置就地显示液位计,工艺操作人员以就地显示液位计为参照判断差压式液位变送器所测量值指示偏高或偏低,因为就地显示液位计比较直观。
而仪表维护人员应根据工艺状况和仪表故障现象进行判断和检查。有关液位(物位)检测故障判断思路可以参照下图进行。
液位仪表系统常见故障处理:
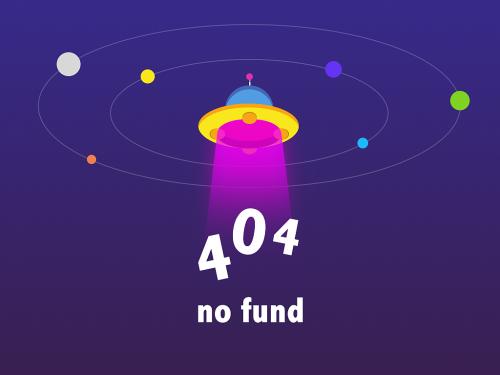
(1)液位突然变大:主要检查变送器负压室引压系统是否堵、泄漏、集气、缺液等。
灌液的具体方法是:
按照停表顺序先停表;
关闭正负压根部阀;
打开正负压排污阀泄压;
打开双室平衡容器灌液丝堵;
打开正负压室排污丝堵;此时液位指示大。
关闭排污阀;
关闭正负压室排污丝堵;
用相同介质缓慢灌入双室平衡容器中,此时微开排污丝堵排气;
直至灌满为止,此时打开正压室丝堵,变送器指示应回零位。
然后按照投表顺序投用变送器。
(2)液位突然变小:主要检查正压室引压系统是否堵、漏、集气、缺液、平衡阀是否关死等。
检查引压系统是否畅通的具体方法是停变送器,开排污阀,检查排污情况(不能外泄的介质除外)。
(3)总控室指示与现场液位不相符:*先判断是不是现场液位计故障,此时可以人为增大或降低液位,根据现场和总控指示情况具体分析问题原因(现场液位计根部阀关闭、堵塞、外漏易引起现场指示不准)。
可以通过检查零点、量程、灌液来恢复液位正常。
如果仍不正常,可通知工艺人员现场监护拆回变送器打压调校。
(4)液位波动频繁:*先和工艺人员结合检查进料、出料情况,确定工艺状况正常后,可通过调整pid参数来稳定。
具体方法是:调节阀投手动状态,先调整设定值与测量值一致,使液位波动平稳下来,再慢慢调整调节阀开度,使液位缓慢上升或下降,达到工艺要求,再调整设定值与测量值一致,待参数稳定后调节阀投自动。
◆ ◆ ◆
简单控制系统故障判断
故障现象:控制系统不稳定,输入信号波动大。
以流量简单控制系统为例,控制系统由双法兰液位变送器、单回路调节器和带电气阀门定位器的气动薄膜调节阀组成。
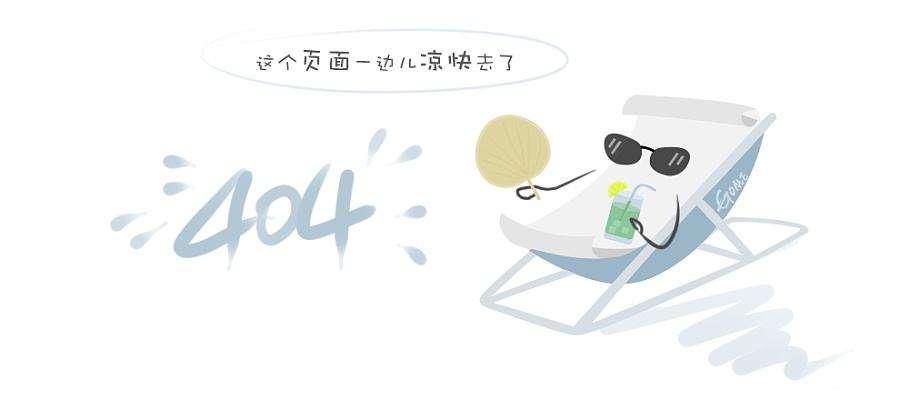
在处理这类故障时,仪表维护人员应很清楚该流量控制系统的组成情况,要了解工艺情况,如工艺介质,简单工艺流程,是加料流量还是出料流量或是塔的回流量。处理故障步骤详见下图。
总之,一旦发现仪表参数有些异常,*先与工艺人员结合,从工艺操作系统和现场仪表系统两方面入手,综合考虑,认真分析,特别要考虑被测参数和控制阀之间的关联,将故障分步分段判定,也就很容易找出问题所在,对症下药解决问题。(本文由九游会ag登录-ag九游会官方网站整理发布,如您在使用仪表的过程中遇到任何问题,都可以致电我司的国内销售服务热线:0517-86917118,我们会有**人员为您答疑解惑)